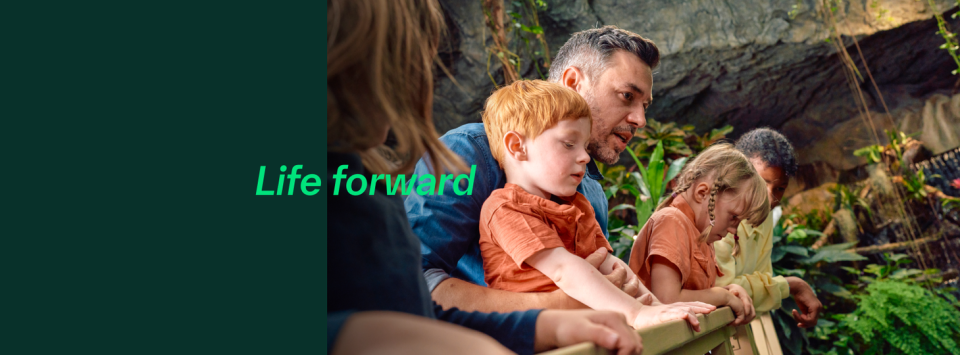
Description
This position will work as a Lean Manufacturing and Six Sigma practitioner in the organization. Will be responsible to lead and execute continuous improvement initiatives in alignment with Site's strategy and objectives. It requires ability to communicate, educate, influence and encourage individuals at all levels in the organization to manage changes towards a competitive, efficient, agile, innovative and lean culture within a high performance organization. The incumbent will manage projects to a successful & timely implementation and realization. Additionally, this position will support new product introductions to optimizing processes, equipment and resources. This position interacts with internal & external personnel from different departments often requiring cross-functional collaboration.
As an employee of Boehringer Ingelheim, you will actively contribute to the discovery, development and delivery of our products to our patients and customers. Our global presence provides opportunity for all employees to collaborate internationally, offering visibility and opportunity to directly contribute to the companies' success. We realize that our strength and competitive advantage lie with our people. We support our employees in a number of ways to foster a healthy working environment, meaningful work, mobility, networking and work-life balance. Our competitive compensation and benefit programs reflect Boehringer Ingelheim's high regard for our employees.
Duties & Responsibilities
- Develops and update Value Stream Mapping as a baseline to identify improvement opportunities to create and deliver value to customers. Creates process flowcharts, analyzes and designs sequence of operations to aim for adequate planning, standardization, organization, simplification, integration, discontinuance, and improved products/processes.
- Drives and conducts analysis pertaining to cost control, cost reduction, inventory control, and effectiveness of production systems. Identifies strengths and weak points, defines and recommends improvement actions, and discuss possible action plans with accountable management. Serves as a culture change agent in all business areas by challenging status quo, identifying opportunities and actively presenting ideas and solutions within a strong continuous improvement mindset.
- Evaluate and sustain tiers meetings within the right context, purpose, and desired outcomes; develops & chooses meaningful metrics & KPI's, and performance charts; leads visual management in all business areas. Develop KPIs Monitors and analyze KPI's, to identify improvement opportunities, enhancing organization performance.
- Communicate/Escalates through the right channels the results of stakeholders analysis that require pro-actively mitigating risks while producing deliverables that support the achievement of outcomes towards business and cultural transformational changes.
- Executes Lean Six Sigma projects, distinguishes between DMAIC, DFSS, PDCA, Kaizens and Kaizen Event opportunities to reduce defects, variability and/or cycle time, increase yield, rates, among others, delivering sustainable results.
- Develops strategic and tactical action plans, communicate, implement and manage adjustments as needed until realization of benefits is achieved in all projects and/or continuous improvement initiatives. Develops lean reporting tools to monitor performance metrics and KPI's.
- Develop and Deliver training, coaching and/or mentoring in Lean Six Sigma tools, Business Process Excellence Tools and processes. Contributes as a consultant to the accomplishment of Business Process Excellence initiatives. Complies with all guidelines, procedures, training, practices, permit conditions, and internal notification of any GMP or EHSS events.
- Support and engage with the overall continuous improvement strategic initiatives by actively participating in all continuous improvement activities, ideas and change management processes.
- Comply with applicable Environmental, Health and Safety (EHS) policies, procedures and actively participate and support all EHS initiatives.
- May perform other duties as assigned.
Requirements
- Bachelor Science (B.S.) in Engineering or Engineering Management from an accredited institution.
- Minimum of two (2) years of relevant experience using Lean Six Sigma & continuous improvement methodologies in regulated manufacturing environment (cGMP).
- Lean Six Sigma Green or Black Belt certification.
- PMP certification desired.
- ASQ certification as CQA or CQE or SQE desirable.
- Experience with Lean/Six Sigma and DMAIC Problem Solving Methodologies.
- Project management skills and experience.
- Advanced knowledge and work experience with Microsoft (Word, Excel, PowerPoint, Outlook, Project), Visio.
- Statistical, Analytical and problem-solving skills.
- Ability to Coach and facilitate individually and at the team level.
- Ability to work cross functionally with direct and indirect influence.
- Excellent oral and written communication skills.
- Fluent in Spanish and English.
- Design Thinking / Agile Method knowledge.
- Knowledge of computers and computer software applications to support the creation and/or modification of automated quality systems.
- Proficient in planning and coordinating project relevant activities.
- Experience with Statistical Softwares (Tableau & Mini Tab desirable).
- Experience working in SAP environment is desired.
Eligibility Requirements
- Must be legally authorized to work in the United States without restriction.
- Must be willing to take a drug test and post-offer physical (if required).
- Must be 18 years of age or older.